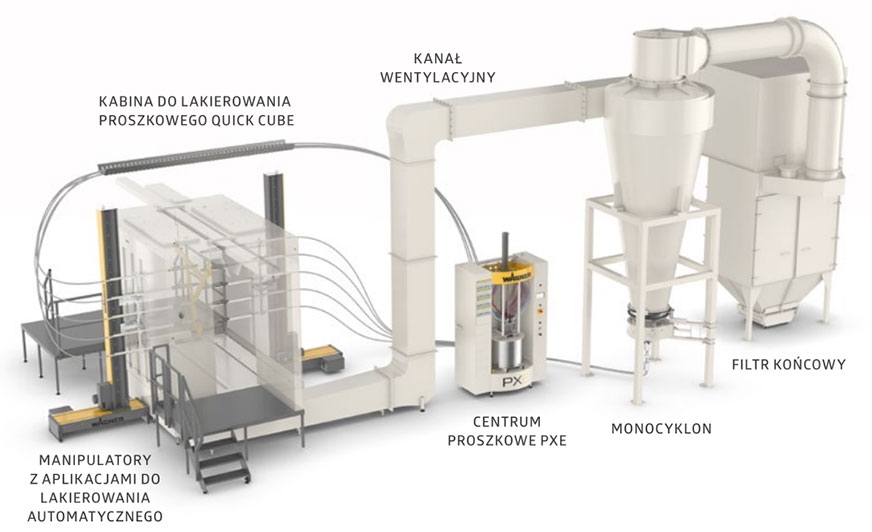
Wydajny monocyklon został połączony z odpowiednio dobranym filtrem za pomocą udoskonalonego systemu kanałów, tworząc koncepcję energooszczędności.
Monocyklon obniża zużycie energii oraz zużycie farby proszkowej
Urządzeniem, które pochłania najwięcej energii w procesie lakierowania proszkowego, jest silnik filtra końcowego, aczkolwiek użycie cyklonu z udoskonaloną technologią przepływu powietrza pozwala zredukować zużycie energii oraz farby, prowadząc do oszczędności w kosztach produkcyjnych.
Systemy do lakierowania proszkowego zużywają energię bezpośrednio w postaci elektrycznej (np. silnik wentylatora, napędy manipulatorów), ale także pośrednio w postaci sprężonego powietrza. Linie Wagnera są wyposażane w energooszczędne komponenty oraz funkcje, takie jak sterowanie aplikacją w przerwach oraz sterowanie wysokością (ilość załączanych aplikacji jest dostosowana do wysokości lakierowanego detalu). Wymienione opcje wyłączają manipulatory i pistolety w przerwach pomiędzy detalami, a włączają je ponownie, gdy detal znajduje się w pobliżu pistoletów proszkowych. Wynikające z tego oszczędności mogą wydawać się niewielkie na pierwszy rzut oka, jednak sumują się do znaczącej wartości w przeciągu roku.
Zmniejszenie kosztów energii o 40 procent
Największą ilość energii w procesie lakierowania proszkowego pochłania silnik wentylatora w filtrze końcowym. Z tego powodu firma Wagner rozwinęła koncepcję energooszczędnej grupy produktów EEP (Energy Efficiency Package) w postaci monocyklonu oraz filtra końcowego. System EEP składa się z monocyklonu, specjalnych kanałów odciągowych i dobranego filtra końcowego.
Co więcej, oprócz oszczędności, udało się również poprawić przepływ powietrza w cyklonie, co zwiększyło jego sprawność o 1-2%. Ten pozytywny „efekt uboczny” pomaga zaoszczędzić do 20% farby.
PUT WAGNER-SERVICE