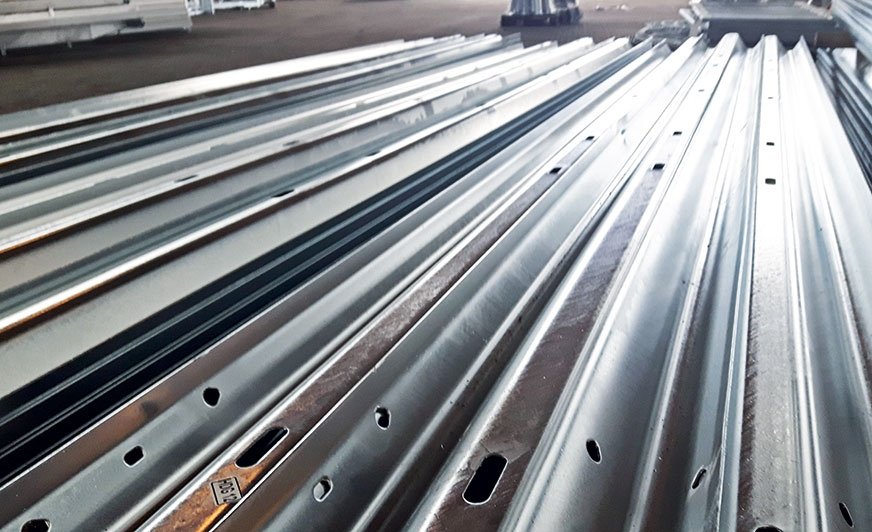
Alternatywa dla klasycznego cynkowania ogniowego
Powłoka cynkowo-aluminiowa charakteryzuje się znacznie lepszą odpornością korozyjną w porównaniu z powłoką cynkową. W dotychczasowej praktyce przemysłowej tego typu zabezpieczenie antykorozyjne wytwarza się jedynie metodą ciągłą na blachach stalowych. FAM S.A., poprzez intensywne badania przemysłowe i prace rozwojowe, podjęło próbę opracowania i wdrożenia technologii wytwarzania powłok Zn-Al na drobnych wyrobach stalowych.
Odporność korozyjna powłoki cynkowej eksploatowanej w bardzo agresywnych warunkach (w atmosferze przemysłowej czy w środowisku morskim) jest niewystarczająca. Szacuje się, że ubytek grubości powłoki w skrajnych warunkach środowiskowych może sięgać nawet 10-20 µm w ciągu roku [1]. Problem stanowi również łączenie elementów ocynkowanych za pomocą śrub, gdzie ze względu na konieczność utrzymania pasowania gwintu, powłoka posiada znacznie mniejszą grubość. W takim połączeniu odpowiedzialny element konstrukcji staje się najsłabszym ogniwem pod względem odporności korozyjnej. Stwarza to konieczność poszukiwania technologii wytwarzania powłok o lepszych właściwościach użytkowych, uzyskanej równie prostą metodą jak ogniowa powłoka cynkowa. Malowanie powłoki metalowej i wytwarzanie w ten sposób systemów duplex stanowi tylko jedną z potencjalnych możliwości zwiększenia trwałości ochrony antykorozyjnej.
W klasycznym, chemicznym procesie przygotowania powierzchni przed metalizacją nie jest możliwe otrzymanie powłoki cynkowo-aluminiowej bez wad powierzchniowych. Powszechnie sądzi się, że ze względu na problemy technologiczne z doborem odpowiedniego topnika, kąpiele cynkowo-aluminiowe nie zostały wprowadzone do metalizacji wyrobów metodą zanurzania pojedynczych wsadów z chemicznym oczyszczaniem powierzchni i topnikowaniem.
Rola aluminium jako dodatku stopowego do kąpieli cynkowej
Jednym z najważniejszych składników stopowych dodawanych od lat do kąpieli w procesie cynkowania ogniowego jest aluminium. Dodatek ten wykorzystywany jest zarówno w metodzie jednostkowej, jak i ciągłej. W metodzie ciągłej aluminium działa hamująco na przebieg reakcji żelaza z ciekłym cynkiem podczas zanurzania elementu w kąpieli. Wykazuje ono względem żelaza większe powinowactwo niż cynk. Przy zawartości powyżej 0,14% w pierwszej kolejności na powierzchni stali tworzą się fazy międzymetaliczne układu Fe-Al (głównie FeAl3). Warstwa faz Fe-Al jest nietrwała i ogranicza na pewien czas powstawanie dyfuzyjnej warstwy przejściowej zbudowanej z kruchych faz układu Fe-Zn [2]. Jest to korzystne ze względu na dalszą przeróbkę plastyczną blach. Zawartość Al w tradycyjnej kąpieli cynkowniczej stosowanej w metodzie ciągłej jest na ogół wyższa od 0,2%. W metodzie zanurzania pojedynczych wsadów dodatki Al w zakresie 0,005-0,02% stosowane są w celu ograniczenia utleniania powierzchni kąpieli. Powstająca na powierzchni cienka zwarta warstwa Al2O3 stanowi barierę dla dostępu tlenu do powierzchni, dzięki czemu zostaje zahamowany proces jej utleniania. Prowadzi to do generowania mniejszej ilości odpadów w postaci popiołu cynkowniczego. Większe ilości Al w kąpieli mogą jednak reagować z topnikiem, powodując nieciągłości powłoki. Dlatego w metodach topnikowych nie należy przekraczać w kąpieli zawartości 0,02% Al.