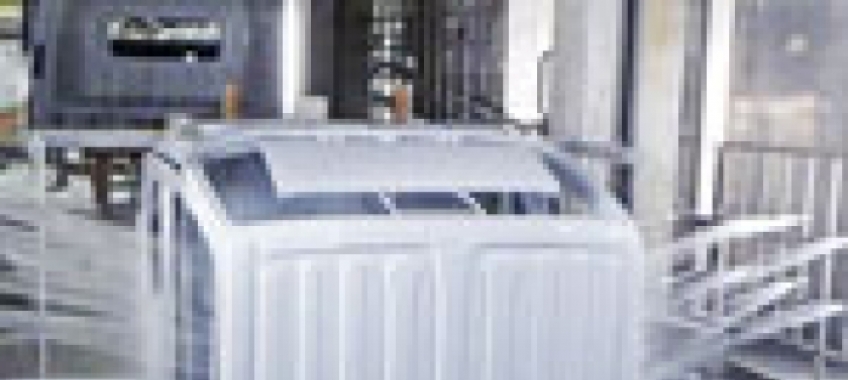
Każdy przenośnik posiada trzy dowolnie programowalne osie i swój własny sterownik. Pozwala to zdefiniować właściwą krzywą zanurzeniową i czasu, które będą dokładnie określone i kontrolowane dla każdego typu kabiny.
Mniej miejsca niż tradycyjne przenośniki łańcuchowe
System pojedynczej pętli E-Shuttle 300 zainstalowany na obszarze zakładu o powierzchni 140 x 24 m nie był tak zaprojektowany, aby pomieścić linię obróbki wstępnej i elektroforezy. - W związku z tym wolne miejsce było bardzo ograniczone, przez co instalacja była trudna - relacjonuje Tamura.
Ale innowacyjne funkcje tego systemu transportowego po raz kolejny okazały się nieocenione: specjalnie zmodyfikowane jego krzywe zanurzalności eliminują potrzebę pochyłości o kącie 45 stopni na wejściu i przy wyjściu, czego wymagają tradycyjne przenośniki wahadłowe. Całkowita długość każdego zbiornika do obróbki może zostać skrócona o długość tych części. Na całej linii technologicznej daje to oszczędność miejsca o około 40 procent. Dodatkową zaletą jest mniejsze zużycie środków do obróbki i innych zasobów (woda, środki chemiczne, energia), które napędzają koszty eksploatacji. - Poprawa efektywności energetycznej i wydajności były jednymi z celów nowej lakierni, która posiada dwie linie lakiernicze - wyjaśnia Tamura. - System E-Shuttle 300 odgrywa ważną rolę w realizacji tych celów.
50 karoserii samochodowych na godzinę
Ze względu na ograniczoną przestrzeń, było nie lada wyzwaniem, aby sprostać docelowej przepustowości Isuzu wynoszącej 50 karoserii na godzinę. Ale w związku z tym inżynierowie wykorzystali proste, elastyczne właściwości programowania krzywej zanurzalności, które umożliwiają przetworzenie każdego zoptymalizowanego kroku tak, aby był wykonywany w jak najkrótszym czasie. Pozycje wszystkich przenośników są stale monitorowane, a ich ruchy koordynowane przez sterownik główny, co zapobiega kolizjom.
Z możliwościami programowania systemu Tamura zapoznał się podczas szkolenia w przedsiębiorstwie Eisenmann w Böblingen. Potrafi on teraz optymalizować krzywe zanurzeniowe, modyfikować je tak, aby uwzględnić zmiany lub zdefiniować zupełnie nowe krzywe dla nowych modeli - u siebie na miejscu i bez pomocy.
Doris Schulz