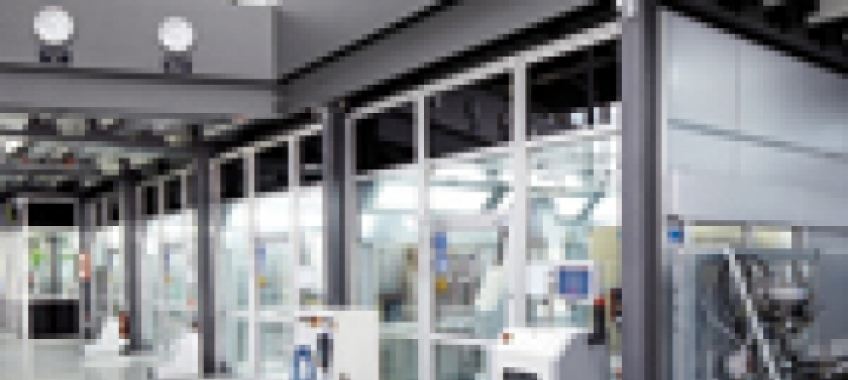
Produkcja farb ciekłych „od kuchni”
Jak wygląda produkcja farb ciekłych jednego największych dostawców na świecie, firmy Mankiewicz? Odwiedziliśmy fabrykę Hamburgu, której produkuje się lakiery sprzedawane na europejskim rynku. Przyjrzyjmy się zatem krok po kroku temu procesowi, wyniku którego powstaje produkt, jaki jest stanie spełnić oczekiwania lakiernika.
Hale produkcyjne zakładu Niemczech, których powstają powłoki na bazie rozpuszczalników powłoki wodorozcieńczalne, wraz nowoczesną linią do produkcji żywic, zajmują 80 tys. metrów kwadratowych powierzchni. Gotowy produkt, czyli tym przypadku farba ciekła, musi charakteryzować się wysoką odpornością antykorozyjną, mechaniczną na różne warunki pogodowe czy chemikalia. Po każdym etapie produkcji lakier przechodzi zatem rygorystyczną kontrolę. Dopiero pozytywne wyniki pozwalają na przejście do kolejnego stadium. To bardzo skomplikowany kontrolowany na każdym etapie proces. Zanim farba trafi do klienta, musi „zaliczyć” fabryce wiele „egzaminów”.
Wstępna kontrola jakości dotyczy wszystkich dodatków do farb, czyli materiałów płynnych suchych (np. pigmentów), które dostarczane są zakładów chemicznych. Każdej partii przypisywany jest numer produktu. Warto zaznaczyć, iż substancje płynne, jak rozpuszczalniki, przechowywane są podziemnych zbiornikach, aby nie stwarzały potencjalnego zagrożenia. pierwszej części hali, gdzie odbierane są od dostawców te składniki, zaczyna się ich selekcjonowanie. Zawsze konkretnej partii naklejany jest numer, który wystarczy później zeskanować, dzięki czemu wiadomo do jakiego typu produkcji ma trafić. To bardzo ważne przy tysiącach ton dostaw, wśród których bardzo łatwo pomyłkę, aby odpowiednio oznakować składniki. Następnym krokiem jest zebranie materiałów ciekłych do procesu automatycznego dozowania, po czym następuje mieszanie dodatków suchych mokrymi. Tak powstała mieszanka jest pompowana za pomocą pompy membranowej do specjalnego młyna, który jest chłodzony. Między jego ścianami częścią chłodzącą jest wąska przestrzeń, przez którą przechodzi farba. Jest ona tam mielona (ważna jest prędkość mielenia, która definiowana jest recepturze danej farby), po czym wypompowywana na zewnątrz. Aby podczas procesu mielenia nie doszło do zniszczenia lakieru, tej przestrzeni między ścianą pompy częścią chłodzącą znajdują się specjalne kulki, które są 3-4 razy twardsze niż diament. Po tym etapie następuje pierwszy proces kontroli lakieru – sprawdza się jak duże są cząstki zmielonej farby. Jeżeli spełnia ona wymagania jakościowe, następuje tzw. wykańczanie farby, czyli dodaje się całą resztę potrzebnych składników. Są to np. stabilizatory lakieru czy dodatki zwiększające połysk. Wówczas zaczyna się inny etap produkcji, mianowicie wybarwianie. Po wstępnym dodaniu pigmentu próbka przekazywana jest do działu kontroli jakości, gdzie badana jest pod kątem koloru oraz parametrów specjalnych dla konkretnej farby. Teraz daną partię towaru czekają kolejne badania jakościowe. dziale analiz kontroli, który dysponuje własnymi laboratoriami, sprawdzane są farby pod kątem różnych odporności. firmie Mankiewicz przykłada się bowiem wielką uwagę do wysokiej jakości wyrobów. – Testujemy lakiery takich samych warunkach, jakich nakładane są lakierniach naszych klientów – mówi Szymon Szumiło, dyrektor firmy Mankiewicz Polsce. – Stąd Hamburgu funkcjonuje centrum techniczne minilakierniami, których pracują różne systemy aplikacji suszenia farb.