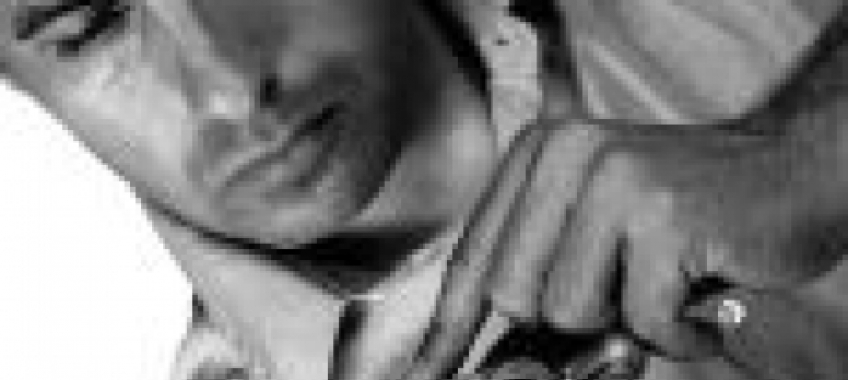
• Konieczność zmodyfikowania czyszczenia i przygotowania powierzchni
• Możliwość stosowania sprawdzonych metod malowania
Magnez, szczególnie dla przemysłu samochodowego, posiada duży potencjał w zakresie ograniczenia masy całkowitej. Ponieważ zarówno proces wytwarzania wyrobu, jak i metody przygotowania powierzchni przed malowaniem muszą być dostosowane do właściwości materiału, dlatego konieczne są odpowiednie technologie. Jednak magnez jako lekki materiał konstrukcyjny w porównaniu z aluminium nie zajmuje jeszcze ugruntowanej pozycji. Powód - koszty dotyczące zapewnienia wystarczającej ochrony korozyjnej są zbyt wysokie dla szerokiego zastosowania.
Magnez jest już stosowany w wielu branżach, w których w pełni wykorzystuje się konstrukcyjne właściwości lekkich materiałów. Do nich należą w pierwszej kolejności branża samochodowa, telekomunikacyjna i elektroniczna. Zmniejszona masa odgrywa pewną rolę w zużyciu energii (części maszyn), zużyciu paliw (transport) czy w urządzeniach przenośnych (laptopy, telefony komórkowe, PDAs).
Magnez jest lekkim, metalicznym materiałem konstrukcyjnym. Przy identycznym elemencie konstrukcyjnym można zaoszczędzić wagowo 40% wobec aluminium i 80% wobec stali. Magnez – metal nieszlachetny jest szeroko dostępny i łatwo poddaje się recyklingowi. Można go obrabiać, można także odlewać kompleksowo drobne części konstrukcyjne o delikatnych strukturach. Przez odlewanie ciśnieniowe można precyzyjnie („na wymiar”) wytwarzać wiele elementów konstrukcyjnych, np felgi, obudowy itp, bez dodatkowej, kosztownej obróbki końcowej. Z powodu swojej niskiej twardości, magnez musi być (tak jak aluminium) wytapiany z dodatkiem innych metali. Dzisiaj stosuje się przeważnie stopy magnezu z dodatkiem aluminium i cynku. Tak wykonane elementy konstrukcyjne, przy takim samym obciążeniu, są lżejsze niż tworzywa sztuczne. Przykładowo, deska rozdzielcza Opla Vectra czy pokrywa bagażnika VW Lupo wykonane są ze stopów magnezu.
Wysoka podatność na korozję
Wybierajac magnez można zmniejszyć masę wyrobu, mamy jednak do czynienia z materiałem o znacznej podatności na korozję. Magnez ulega samopasywacji i jest niestabilny zarówno wobec niskich jak i wysokich wartości pH, podlega wpływowi jonów chlorku i innych podobnych jonów. Stąd, niezbędne jest staranne przygotowanie powierzchni jako warunek konieczny do nakładania następnych warstw. Tylko w ten sposób można zapewnić elementom konstrukcyjnym z magnezu wystarczającą ochroną przeciwkorozyjną. Jednocześnie dajemy dobrze przyczepne podłoże dla farb i lakierów, które gwarantują twarde, odporne na zadrapania uszlachetnienie powierzchni. Podobnie jak i dla innych metali, także do obróbki magnezu są dzisiaj do dyspozycji metody bez chromu sześciowartościowego: anodowanie, pasywacja, przygotowanie powierzchni pod połączenia klejowe, powłoki konwersyjne jako podłoże dla farb i lakierów (np. na bazie organicznego silanu albo fluorku cyrkonu) jak powłoki proszkowe czy powłoki z farb ciekłych. Aktualne badania zajmują się ochronnymi powłokami przeciwkorozyjnymi na bazie „nano-kompozytów”. Do dlaszej obróbki można stosować sprawdzone technologie malowania i standardowe urządzenia do suszenia dla zwykle stosowanych materiałów malarsko-lakierniczych. Szerokie zastosowanie magnezu, często jednak jest skazane na niepowodzenie ze względu na zbyt wysokie koszty przygotowania powierzchni.