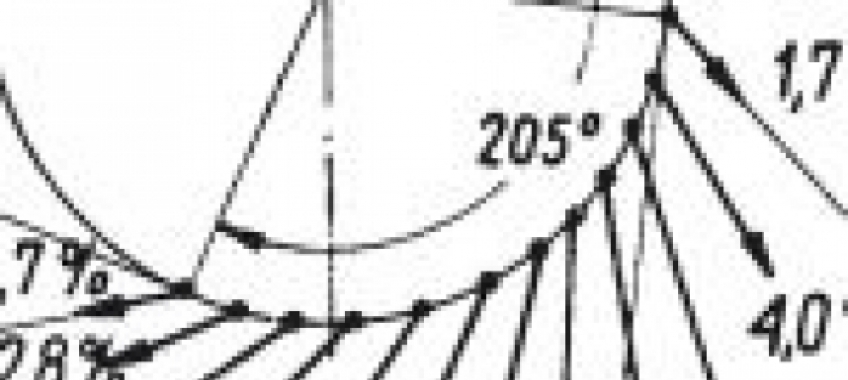
Podstawową metodą oczyszczania i przygotowania powierzchni jest obróbka strumieniowo-ścierna. Do prowadzenia tej obróbki są stosowane głównie oczyszczarki wirnikowe miotające, odpowiednio dobrany śrut. Zagadnienie jakości i właściwego doboru śrutu ma istotne znaczenie ze względu na korelację uzyskiwanych efektów – jakości powierzchni wyrobów ze zużyciem śrutu z kosztami oczyszczania odlewów.
Charakterystyka stosowanego śrutu, zasady doboru
W odlewnictwie stopów żelaza podstawowym ścierniwem jest śrut metalowy. Wymagania techniczne dotyczące metalowych ścierniw stosowanych w obróbce strumieniowo-ściernej określa Polska Norma PN-EN ISO 11124-1. Powszechnie stosowane ścierniwa określone wyżej podaną normą zawiera tablica 1.
Tablica 1. Powszechnie stosowane ścierniwa w obróbce strumieniowo-ściernej [12].
Zgodnie z normą oznaczenie ścierniwa powinno zawierać informacje określające jego podstawowe parametry. Dla przykładu, oznaczenie: ścierniwo PN ISO11124M/HCS/G140-710-HV - oznacza ścierniwo metalowe z wysokowęglowego staliwa odpowiadające wymaganiom odpowiedniego arkusza ISO11124 o wyjściowym ostrokątnym kształcie ziarna, granulacji nominalnej ziaren ściernych 1,40 mm i twardości w zakresie od 570 HV do 710 HV. Szczegółowe wymagania dotyczące poszczególnych rodzajów podanych ścierniw zawierają odpowiednie arkusze PN-EN ISO 11124. Określają one między innymi: minimalną twardość ziaren, rodzaje wad i ich dopuszczalny udział, wymaganą strukturę ziaren, skład chemiczny.Dokonując doboru gatunku, rodzaju i granulacji śrutu, należy brać pod uwagę następujące czynniki: rodzaj i kształt przedmiotu, w tym jego podatność na deformację, rodzaj i wielkość zanieczyszczenia przedmiotu, wymagany stopień czystości powierzchni po oczyszczeniu, wymaganą chropowatość powierzchni po oczyszczeniu, wymagany profil chropowatości, wymaganą wydajność oczyszczania, wpływ użytego śrutu na koszty oczyszczania.
Rys.1. Ciężar rozrzutu śrutu (w % całkowitej ilości wyrzucanego śrutu). Koło rzutowe o średnicy 500 mm, 8 promieniowych łopatek, łopatki robocze cofnięte o 15o względem łopatek wirnika, ilość doprowadzanego śrutu 90 kg/min
Doboru rodzaju i granulacji śrutu dokonuje się najczęściej na zasadzie kompromisu, na przykład dokonując wyboru pomiędzy energią śrutu i związaną z nią wydajnością, a chropowatością powierzchni. Dla uzyskania dobrego efektu oczyszczania istotnym jest, aby śrut będący w obiegu oczyszczarki tworzył odpowiednią mieszaninę różnych granulacji (rys. 5). W mieszaninie zadaniem śrutu o dużej granulacji jest zgrubne oczyszczenie powierzchni i usunięcie nadmiaru masy. Śrut o granulacji średniej i małej ma za zadanie dokładne oczyszczenie powierzchni, a w szczególności wgłębień w powierzchni przedmiotów. Stąd też przy pierwszym napełnieniu oczyszczarki należy wsypać śrut w następującej proporcji: 60% śrutu o przyjętej największej granulacji, 20% śrutu o granulacji niższej o jeden stopień i 10% śrutu o granulacji niższej o kolejny stopień. Przy pierwszym uzupełnianiu śrutu w obiegu oczyszczarki zaleca się podać mieszankę w następującej proporcji: 70% śrutu o największej przyjętej granulacji i 30% śrutu o granulacji niższej o jeden stopień. W trakcie dalszej eksploatacji odpowiednia mieszanina powstaje w sposób samoczynny i dalsze uzupełnienia powinny polegać na podawaniu do obiegu oczyszczarki śrutu o największej przyjętej granulacji.