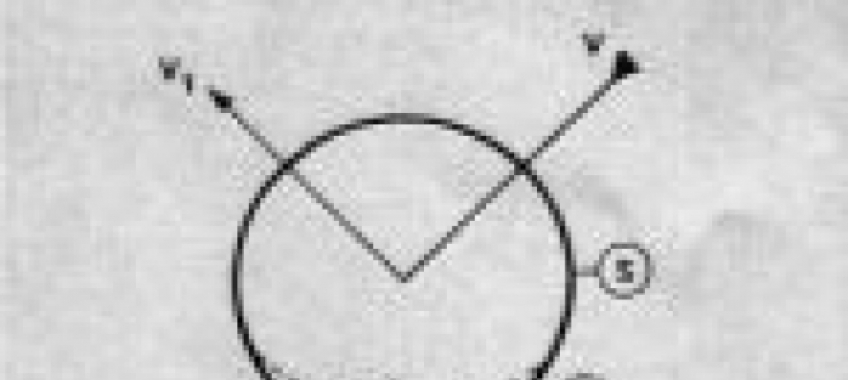
Najnowsze osiągnięcie produkcji ścierniw metalowych, przeznaczonych do obróbki strumieniowo-ściernej powierzchni
Śrut staliwny niskowęglowy jest najnowszym osiągnięciem przemysłu wytwarzającego śruty. Etapami rozwoju ścierniw metalowych były: najpierw śruty z żeliwna utwardzonego, następnie śruty stalowe cięte z drutu, śruty staliwne wysokowęglowe obrobione cieplnie, aż do śrutu staliwnego niskowęglowego znanego od 1960 roku. Był to efekt poszukiwań śrutu zbliżonego do trwałości śrutu ciętego z drutu stalowego, równie wydajnego co śrut staliwny wysokowęglowy uszlachetniany cieplnie, pozwalającego uzyskiwać wysoką jakość powierzchni obrabianej, mniej przy tym agresywnego dla elementów roboczych rzucających śrut (łopatki kół rzutowych, przewody podające ścierniwo do koła rzutowego, wirniki rozdzielaczy, tuleje regulacyjne). Śrut niskowęglowy produkowany jest w procesie topienia w piecach indukcyjnych, pociętych, czystych, wysokogatunkowych blach głęboko tłocznych ze stali podeutektycznej z niską zawartością węgla (C), fosforu (P) i siarki (S) oraz czystych, precyzyjnie dozowanych dodatków stopowych. Uzyskuje się staliwo niskowęglowe o procentowym składzie wagowym pokazanym w tabeli 1.
Tabela 1. Skład chemiczny śrutu niskowęglowego z POLMINERALU na tle normy śrutu wysokowęglowego
w % wagowych.
Zestawienie pokazuje, że w śrutach niskowęglowych znajduje się zdecydowanie mniej węgla i zanieczyszczeń siarką oraz fosforem niż w śrutach wysokowęglowych. Niska zawartość węgla sprawia, iż śrut ten jest bardziej plastyczny oraz nie tworzy na powierzchni ziaren, twardej grubej warstwy węglików, skłonnych do pęknięć a jedynie nanowarstwy takich węglików. Dlatego norma na śruty niskowęglowe nie przewiduje występowania wad w postaci pęknięć powierzchniowych. Norma na śruty wysokowęglowe przewiduje natomiast do 15 % wad w postaci pękniętych ziaren śrutu okrągłego.
Śrut niskowęglowy
Śrut wysokowęglowy
Fotografia 1. Przekrój ziarna śrutu niskowęglowego i wysokowęglowego (po prawej).
Fotografia 1 pokazuje poglądowo tę różnicę miedzy oboma rodzajami śrutów na przekroju ziaren śrutu niskowęglowego i wysokowęglowego. Brak skłonności do pęknięć ziaren śrutu niskowęglowego jest główną przyczyną jego wyższej trwałości od 10 do 40 % od śrutu staliwnego (średnio 20 %). Fakt ten powoduje, że proces zużywania się ziaren śrutów niskowęglowych jest odmienny od śrutów wysokowęglowych i następuje jedynie w wyniku ścierania się powierzchniowego.Rysunek 1. Mechanizm zmniejszania się ziaren śrutów wysokowęglowych według I. Horowitza.