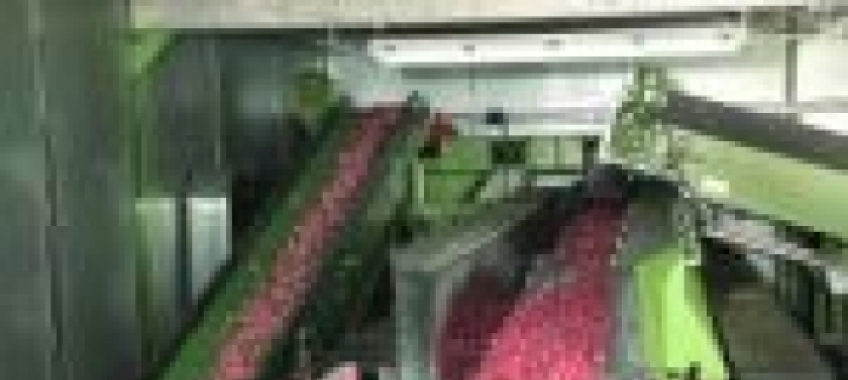
Usuwanie wypływek z obrabianych elementów w urządzeniach przelotowych
Na świecie jest niewielu producentów samochodów, którzy nie otrzymują zewnętrznych lusterek lub przynajmniej części do nich od firmy Visiocorp Deutschland GmbH (wcześniej Schefenacker Mirrors GmbH), która ma swoją siedzibę w Schwaikheim w Szwabii. Przedsiębiorstwo to zajmuje się nie tylko rozwojem, budową wzorów i konstruowaniem lusterek, wykonuje ono także odlewy ciśnieniowe ze stopów aluminium wsporników lusterek i systemów stóp lusterek dla zakładów montażowych na całym świecie.
- Aby zapewnić konkurencyjność zakładów zlokalizowanych w Niemczech, konieczne było wdrożenie całkowicie automatycznej produkcji - twierdzi Christian Barth, kierownik produkcji w Visiocorp.
Wysokie wymagania
Po zakończeniu obróbki wibrościernej, elementy składowe lusterek są lakierowane albo poddawane dalszej obróbce powierzchniowej. W obu przypadkach wymagana jest jednorodna powierzchnia, wolna od zadziorów oraz odtłuszczona. Instalacja musi być w stanie poddać obróbce całą paletę ponad 100 różnych części o masie od 50 g do 2500 g.Optymalna cyrkulacja kształtek i obrabianych przedmiotów w zbiorniku roboczym zapewnia stałą jakość obróbki. Powrót kształtek z tworzywa sztucznego do procesu odbywa się z wykorzystaniem transportera taśmowego (z lewej strony).
- Dla nas bardzo ważnymi aspektami był wysoki efekt racjonalizacyjny, odpowiednia przepustowość, wysoka dyspozycyjność linii w 18 godzin na dobę oraz długa żywotność, jak również dopasowanie do lokalnych warunków - opisuje najważniejsze kryteria Christian Barth. W tym celu, jako podstawową instalację, przyjęto korytowe, przelotowe urządzenie typu R 550/4600 DA. Instalacja ta jest zintegrowana z procesem produkcji, a dla odciążenia od hałasu znajdujących się w pobliżu miejsc pracy ręcznej, została obudowana kabiną dźwiękoszczelną. Redukuje ona poziom hałasu do 78 dB(A).
Całkowicie automatyczne doprowadzenie
Doskonale dopracowana logistyka obrabianych części doprowadza po odlewaniu wrażliwe na uszkodzenia części do instalacji do obróbki wibrościernej, wykorzystując w tym celu specjalną “windę”. Dzięki temu nakłady na transport wewnętrzny oraz na siłę roboczą są zredukowane do minimum. W sterownikach PLC instalacji zapisano 20 programów, co pozwala na optymalną obróbkę różnych części. Winda transportuje obrabiane części na pierwsze piętro i obraca pojemnik z częściami o 180°. Mechanizm podtrzymujący nie pozwala na wcześniejsze wypadnięcie części, co spowodowałoby ich wzajemne uszkodzenie. Po osiągnięciu położenia końcowego, obrabiane części są przekazywane do bufora części, co pozwala na ich szczególnie delikatną manipulację.